News and Events
•••Hot news
•••-
The key to ensure the long-term stable operation of the standard inverter DC arc welding machine
-
Welding Parameters Optimization and quality Control of Stainless Steel MIG Welding Wire
-
Advancements in Welding Electrode Technology and Their Impact on the Industry
-
Troubleshooting Common Issues with Welding Electrodes and Their Solutions
-
An In-depth Look into the Raw Materials and Manufacturing Processes of Carbon Steel MIG Welding Wires
Five Invisible Problems In Steel Structure Welding!
Mar 03,2025
1. The transition is not smooth, when plates of different thicknesses are butt-jointed
When butt-joining plates of different thicknesses and widths, pay attention to whether the thickness difference of the plates is within the standard allowable range. If it is not within the allowable range and a smooth transition is not performed, the weld is likely to cause stress concentration and welding defects such as lack of fusion at the place where the weld exceeds the thickness of the thin plate, affecting the welding quality.
Solution:
When the relevant regulations are exceeded, the weld should be welded into a slope, and the maximum allowable slope should be 1:2.5; or one or both sides of the thickness should be processed into a slope before welding, and the maximum allowable slope should be 1:2.5. When the structure directly bears dynamic loads and needs fatigue verification, the slope should not be greater than 1:4. When plates of different widths are butt-jointed, thermal cutting, mechanical processing or grinding wheel grinding should be used to make a smooth transition according to factory and site conditions, and the maximum allowable slope of the joint is 1:2.5.
2. Multi-layer welding is discontinuous, resulting in cold cracks
When welding thick plates in multiple layers, if you do not pay attention to the temperature control between layers, such as the interval time between layers is too long, welding without reheating will easily cause cold cracks between layers; if the interval time is too short and the interlayer temperature is too high (over 900°C), it will also affect the performance of the weld and heat-affected zone, causing coarse grains, resulting in reduced toughness and plasticity, and leaving potential hidden dangers to the joints.
Solution:
When welding thick plates in multiple layers, the temperature between layers should be controlled more strictly. The temperature of the base metal to be welded should be checked during continuous welding to ensure that the temperature between layers is consistent with the preheating temperature as much as possible. The maximum temperature between layers should also be controlled. The welding time should not be too long. If welding is interrupted, appropriate post-heating and heat preservation measures should be taken. When welding again, the re-preheating temperature should be appropriately higher than the initial preheating temperature.
3. Welding deformation
When welding, didn't pay attention to controlling deformation from aspects such as welding sequence, personnel arrangement, groove form, selection of welding specifications and operation methods, which leads to large deformation after welding, difficulty in correction and increased costs, especially for thick plates and large workpieces, which are difficult to correct. Mechanical correction can easily cause cracks or layered tearing. The cost of flame correction is high and improper operation can easily cause overheating of the workpiece. For workpieces with high precision requirements, if effective deformation control measures are not taken, the installation size of the workpiece will not meet the use requirements, and even cause rework or scrapping.
Solution:
Adopt a reasonable welding sequence and select appropriate welding specifications and operating methods, and also adopt anti-deformation and rigid fixation measures.
4. The weld angle size of the butt joint or corner butt joint combination weld is not enough for full penetration
If the weld leg size of the butt or corner butt combination welds that require full penetration, such as T-joints, cross joints, corner joints, etc., is not enough, or the weld leg size of the web and upper wing edge connection welds of crane beams or similar components designed with fatigue verification requirements is not enough, the strength and stiffness of the welding will not meet the design requirements.
Solution:
T-joints, cross joints, corner joints and other butt joints that require full penetration must have sufficient weld leg requirements according to design requirements. Generally, the weld leg size should not be less than 0.25t (t is the thickness of the thinner plate at the connection). The weld leg size of the crane beam or similar web and upper flange connection weld with fatigue calculation requirements is 0.5t and should not be greater than 10mm. The allowable deviation of the welding size is 0 to 4 mm.
5. Welding the joint gap with the welding rod head or iron block
Since it is difficult to fuse the electrode head or iron block with the welded part during welding, welding defects such as lack of fusion and lack of penetration will occur, reducing the connection strength. If rusty electrode heads or iron blocks are used for filling, it is difficult to ensure that the material is consistent with the parent material; if electrode heads or iron blocks with oil stains and impurities are used for filling, defects such as pores, slag inclusions, and cracks will appear in the weld. These situations will greatly reduce the quality of the weld of the joint and fail to meet the quality requirements of the weld in the design and specifications.
Solution:
(1) When the workpiece assembly gap is large, but does not exceed the specified allowable range, and the assembly gap exceeds 2 times the thickness of the thin plate or is greater than 20mm, the surfacing method should be used to fill the concave part or reduce the assembly gap. It is strictly forbidden to use the method of filling the joint gap with the electrode head or iron block for repair welding.
(2) When processing and marking parts, pay attention to leaving enough cutting allowance and welding shrinkage allowance after cutting, control the size of the parts, and do not increase the gap to ensure the overall size.
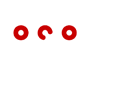
And what can we do for you?
Do you have questions about the cetecom advanced services, are you interested in a consultation or would you like to get a concrete offer? Just contact us directly. Our team of experts is looking forward to your message.

We offer a variety of top-quality welding consumables, welding accessories, welding machine for shipbuilding, aviation, nuclear power, pipeline, pressure vessel, steel structure, container, engineering machinery etc.
- Products Welding Consumables Welding Machine
- Solutions Welding Consumables Welding Machine
- quick links Cases News & Events Company
-
Contact
Email: info@tsuntec.com
Telephone:+86 150 6396 2790
whatsapp: 8615063962790
Address:No 2 South Hei Long Jiang Road, Shibei District, Qingdao, China