News and Events
•••Hot news
•••-
The key to ensure the long-term stable operation of the standard inverter DC arc welding machine
-
Welding Parameters Optimization and quality Control of Stainless Steel MIG Welding Wire
-
Advancements in Welding Electrode Technology and Their Impact on the Industry
-
Troubleshooting Common Issues with Welding Electrodes and Their Solutions
-
An In-depth Look into the Raw Materials and Manufacturing Processes of Carbon Steel MIG Welding Wires
Carbon Steel Welding Wire for Pipeline Projects
Feb 28,2025
Pipe projects are among the most critical and demanding engineering applications, requiring high-quality materials, precise welding techniques, and reliable solutions to ensure longevity and performance under various operating conditions. Carbon steel welding wire has become a cornerstone in pipeline construction due to its strength, durability, and versatility. This guide will delve into the key aspects of carbon steel welding wire, its applications in pipeline projects, and how to make an informed decision for your next project.
The Importance of Carbon Steel Welding Wire in Pipeline Projects
Carbon steel is one of the most widely used materials in pipeline construction due to its cost-effectiveness, availability, and excellent mechanical properties. It is particularly suited for high-stress applications, such as pipelines that operate under high pressure or temperatures. When it comes to welding, carbon steel requires a specific type of welding wire to ensure optimal fusion and strength.
The choice of welding wire can significantly impact the overall performance and longevity of a pipeline. Factors such as tensile strength, ductility, chemical composition, and corrosion resistance must be carefully considered to match the project's requirements. For instance, pipelines in high-temperature environments may require weld wires with higher heat resistance, while those in corrosive conditions need wires that can withstand rusting.
Key Characteristics of Carbon Steel Welding Wire for Pipelines
Tensile Strength: Pipeline welds must withstand extreme pressure and stress, so the welding wire should have high tensile strength to ensure integrity under load.
Corrosion Resistance: Pipelines are often exposed to harsh environmental conditions, including moisture, salts, and chemicals. The welding wire must have a protective coating or chemical composition that prevents rusting and ensures long-term durability.
Ductility: Welds in pipelines often experience thermal expansion and contraction, so the weld wire must be malleable enough to accommodate these changes without cracking or breaking.
Electrode Compatibility: The welding wire must be compatible with the type of welding equipment being used, such as MIG (Metal Inert Gas), TIG (Tungsten Inert Gas), or Stick electrodes.
Chemical Composition: The right chemical composition ensures that the welds are strong and free from defects like porosity or inclusion of impurities.
Types of Carbon Steel Welding Wire for Pipeline Projects
There are several types of carbon steel welding wire available, each suited for specific applications in pipeline projects. Below is a breakdown of the most common types:
E701-11: This is one of the most commonly used electrodes for carbon steel welding. It has excellent strength and durability, making it ideal for heavy-duty pipelines.
ER707: A low-carbon steel wire with high tensile strength, often used in construction and pipeline projects due to its strong resistance to impact fractures.
E750: Designed for applications requiring high tensile strength and excellent welding properties, this wire is commonly used in pressure pipelines and other critical infrastructure.
E911: A advanced hollow-copper electrode designed for multi-pass welding and complex joints in pipelines. It provides superior control over the welding process and consistent results.
ER535: A high Mn (Manganese) steel wire that offers excellent weldability and strength, particularly useful in high-temperature environments.
Best Practices for Selecting Carbon Steel Welding Wire
Match the Project Requirements: Always refer to the project specifications and material requirements to select the appropriate welding wire. Consider factors like pressure, temperature, and environment.
Consider Corrosion Resistance: If the pipeline is exposed to aggressive chemicals or salty environments, choose a welding wire with a protective coating or high corrosion resistance.
Check Welding Equipment Compatibility: Ensure that the welding wire is compatible with your existing equipment, whether MIG, TIG, or Stick.
Trial Warranties: Request trial welds to assess the quality and performance of the wire before committing to large orders.
Consult Manufacturer Specifications: Always review the technical data sheets provided by the manufacturer to ensure that the welding wire meets industry standards and certifications.
Applications of Carbon Steel Welding Wire in Pipeline Projects
Oil and Gas Pipelines: pipelines transporting oil and natural gas often require carbon steel due to their high-stress nature. The welding wire must be able to handle the weight, pressure, and potentially harsh operating conditions.
Water Transmission Systems: These pipelines may also be constructed from carbon steel, with welders requiring wires that can withstand corrosion and thermal expansion.
Utility Lines: Low-carbon steel welding wires are frequently used in utility pipelines due to their balance of strength and cost-effectiveness.
Industrial Applications: Manufacturers rely on carbon steel for pipeline projects in industrial settings, where the welds need to be both strong and durable.
Construction Projects: Carbon steel is a popular choice for temporary pipeline solutions during construction, as it provides a cost-effective and sturdy solution.
Ensuring High-Quality Welds: Tips for Using Carbon Steel Welding Wire
Preheating: Proper preheating is essential to ensure that the base metal reaches the correct temperature before welding begins. This minimizes the risk of cracking or porosity.
Polarity Settings: Adjust the polarity settings on your MIG welder according to the type of welding wire being used to achieve optimal arc quality and weld penetration.
Cooling Post-Welding: After completing the weld, allow the area to cool down naturally. Sudden cooling can cause thermal stress cracks, which weaken the weld over time.
Inspection: Conduct thorough inspections of the welds using non-destructive testing methods like X-ray or ultrasonic testing to ensure there are no defects or weaknesses.
Documentation: Maintain detailed records of the welding process and results for future reference and quality control purposes.
Compliance with Industry Standards
When working on pipeline projects, it's crucial to adhere to industry standards such as API (American Petroleum Institute), ASTM, and ISO. These standards dictate the acceptable levels of tensile strength, elongation, and other mechanical properties required for the welding wire. Ensure that the wire you select meets these requirements.
Summary
Selecting the right carbon steel welding wire is critical to ensuring the success of your pipeline project. By considering factors like tensile strength, corrosion resistance, and compatibility with your equipment, you can choose a wire that delivers reliable performance under challenging conditions. Always consult with manufacturers, review project specifications, and conduct trial welds to make an informed decision.
By following best practices and prioritizing quality, you can ensure that your pipeline projects meet all safety and durability requirements, providing long-term value for stakeholders.
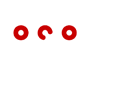
And what can we do for you?
Do you have questions about the cetecom advanced services, are you interested in a consultation or would you like to get a concrete offer? Just contact us directly. Our team of experts is looking forward to your message.

We offer a variety of top-quality welding consumables, welding accessories, welding machine for shipbuilding, aviation, nuclear power, pipeline, pressure vessel, steel structure, container, engineering machinery etc.
- Products Welding Consumables Welding Machine
- Solutions Welding Consumables Welding Machine
- quick links Cases News & Events Company
-
Contact
Email: info@tsuntec.com
Telephone:+86 150 6396 2790
whatsapp: 8615063962790
Address:No 2 South Hei Long Jiang Road, Shibei District, Qingdao, China