News and Events
•••Hot news
•••-
The key to ensure the long-term stable operation of the standard inverter DC arc welding machine
-
Welding Parameters Optimization and quality Control of Stainless Steel MIG Welding Wire
-
Advancements in Welding Electrode Technology and Their Impact on the Industry
-
Troubleshooting Common Issues with Welding Electrodes and Their Solutions
-
An In-depth Look into the Raw Materials and Manufacturing Processes of Carbon Steel MIG Welding Wires
An In-depth Look into the Raw Materials and Manufacturing Processes of Carbon Steel MIG Welding Wires
Nov 29,2024
Carbon Steel MIG Welding Wires are essential in various welding applications due to their high strength, durability, and adaptability. Understanding the raw materials and manufacturing processes behind these wires is crucial for ensuring their quality and performance.
Raw Materials
The primary raw material for Carbon Steel MIG Welding Wires is carbon steel. Carbon steel is an alloy of iron that contains a small percentage of carbon, typically ranging from 0.05% to 2.1% by weight. It may also contain other alloying elements such as manganese, silicon, and small amounts of sulfur and phosphorus.
The choice of carbon steel grade for MIG welding wires depends on the intended application and the required properties of the weld. For example, low-carbon steels are often used for general welding purposes due to their good weldability and formability. Medium-carbon steels offer higher strength and hardness but may be less weldable. High-carbon steels are used for applications requiring high wear resistance and hardness but are generally more difficult to weld.
Manufacturing Processes
The manufacturing process for Carbon Steel MIG Welding Wires involves several steps, including raw material preparation, wire drawing, coating, and packaging.
Raw Material Preparation
The raw carbon steel material is first inspected to ensure it meets the required specifications and standards.
The material is then cleaned to remove any impurities, oxides, or scale that may affect the welding process or the quality of the weld.
Wire Drawing
The cleaned carbon steel material is fed into a wire drawing machine, which reduces its diameter to the desired size for MIG welding wires.
The drawing process may involve multiple stages of reduction, with each stage using progressively smaller dies to achieve the final wire diameter.
Coating
Many Carbon Steel MIG Welding Wires are coated with a flux or lubricant to improve their welding performance.
The coating helps to protect the wire from contamination during storage and transportation and can also enhance the wettability and fluidity of the molten weld pool.
The coating material and thickness are carefully selected based on the intended application and welding conditions.
Packaging
The coated wire is then wound onto plastic or metal spools for easy handling and storage.
The spools are usually labeled with information about the wire's diameter, material, and manufacturer.
The packaging may also include instructions for storage, transportation, and handling to ensure the wire remains in good condition until use.
Quality Control
Throughout the manufacturing process, rigorous quality control measures are taken to ensure that the Carbon Steel MIG Welding Wires meet the required specifications and standards. This includes inspections at various stages of production, testing of the final product, and certification to ensure compliance with industry standards.
In conclusion, the raw materials and manufacturing processes of Carbon Steel MIG Welding Wires play a crucial role in determining their quality and performance. By using high-quality carbon steel and adhering to rigorous manufacturing processes, manufacturers can produce welding wires that meet the needs of various welding applications.
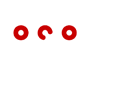
And what can we do for you?
Do you have questions about the cetecom advanced services, are you interested in a consultation or would you like to get a concrete offer? Just contact us directly. Our team of experts is looking forward to your message.

We offer a variety of top-quality welding consumables, welding accessories, welding machine for shipbuilding, aviation, nuclear power, pipeline, pressure vessel, steel structure, container, engineering machinery etc.
- Products Welding Consumables Welding Machine
- Solutions Welding Consumables Welding Machine
- quick links Cases News & Events Company
-
Contact
Email: info@tsuntec.com
Telephone:+86 150 6396 2790
whatsapp: 8615063962790
Address:No 2 South Hei Long Jiang Road, Shibei District, Qingdao, China