News and Events
•••Hot news
•••-
The key to ensure the long-term stable operation of the standard inverter DC arc welding machine
-
Welding Parameters Optimization and quality Control of Stainless Steel MIG Welding Wire
-
Advancements in Welding Electrode Technology and Their Impact on the Industry
-
Troubleshooting Common Issues with Welding Electrodes and Their Solutions
-
An In-depth Look into the Raw Materials and Manufacturing Processes of Carbon Steel MIG Welding Wires
Troubleshooting Common Issues with Welding Electrodes and Their Solutions
Nov 29,2024
Troubleshooting Common Issues with Welding Electrodes and Their Solutions" is a crucial topic for welders and welding professionals. Below are some common issues that can arise with welding electrodes, along with their solutions:
1. Arc Blow
Issue: Arc blow occurs when magnetic fields interfere with the welding arc, causing it to wander or be unstable. This can lead to poor weld quality and increased porosity.
Solution: To minimize arc blow, use electrodes with low magnetic permeability, such as those made from non-magnetic materials. Additionally, ensuring proper grounding and shielding of the welding area can help reduce magnetic interference.
2. Sticking of the Electrode
Issue: Sticking of the electrode to the workpiece can occur when the welding current is too low or the electrode is not properly inserted into the welding gun.
Solution: Increase the welding current to ensure sufficient heat is generated to melt the electrode and base material. Also, ensure that the electrode is properly inserted and held securely in the welding gun.
3. Excessive Spatter
Issue: Excessive spatter can occur due to improper welding parameters, contaminated electrodes, or poor electrode quality.
Solution: Optimize welding parameters such as welding current, voltage, and electrode stick-out length. Use clean, high-quality electrodes and avoid using electrodes that are too old or damaged.
4. Poor Weld Penetration
Issue: Poor weld penetration can be caused by insufficient welding current, incorrect electrode angle, or excessive electrode travel speed.
Solution: Increase the welding current to ensure sufficient heat input. Adjust the electrode angle to be more perpendicular to the workpiece. Reduce electrode travel speed to allow more time for heat to penetrate the base material.
5. Cracking in the Weld
Issue: Cracking in the weld can occur due to excessive stress in the weldment, improper electrode selection, or poor welding technique.
Solution: Use electrodes that are compatible with the base material and welding conditions. Preheat the workpiece to reduce stress and improve weldability. Use proper welding techniques such as layer welding or step welding to minimize stress concentrations.
6. Contamination of the Weld
Issue: Contamination of the weld can occur due to dirty electrodes, contaminated workpieces, or improper shielding gas flow.
Solution: Use clean electrodes and ensure that the workpiece is free of dirt, grease, and other contaminants. Use proper shielding gas flow rates and ensure that the gas covers the welding area adequately.
7. Incorrect Electrode Size
Issue: Using an incorrect electrode size can lead to improper welding parameters and poor weld quality.
Solution: Select the correct electrode size based on the welding current, electrode material, and welding conditions. Consult welding charts or consult with a welding professional to ensure proper electrode selection.
8. Wear and Tear of the Electrode
Issue: Wear and tear of the electrode can occur due to excessive use, improper storage, or exposure to harsh environments.
Solution: Store electrodes in a dry, cool place to prevent rust and corrosion. Replace worn-out electrodes regularly and avoid using electrodes that are too old or damaged.
9. Incorrect Welding Position
Issue: Welding in the incorrect position can lead to poor weld quality and increased risk of weld defects.
Solution: Use proper welding positions such as flat, horizontal, vertical, or overhead welding. Use welding jigs or fixtures to hold the workpiece in the correct position during welding.
10. Electrode Tip Clogging
Issue: Electrode tip clogging can occur due to impurities in the electrode or welding current fluctuations.
Solution: Use high-quality electrodes and ensure that the welding current is stable. Clean the electrode tip regularly to remove any impurities or debris that may cause clogging.
By addressing these common issues and implementing the corresponding solutions, welders can improve weld quality, reduce defects, and increase productivity. Always consult welding charts, welding procedures, and welding professionals to ensure proper electrode selection and welding techniques.
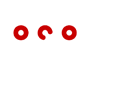
And what can we do for you?
Do you have questions about the cetecom advanced services, are you interested in a consultation or would you like to get a concrete offer? Just contact us directly. Our team of experts is looking forward to your message.

We offer a variety of top-quality welding consumables, welding accessories, welding machine for shipbuilding, aviation, nuclear power, pipeline, pressure vessel, steel structure, container, engineering machinery etc.
- Products Welding Consumables Welding Machine
- Solutions Welding Consumables Welding Machine
- quick links Cases News & Events Company
-
Contact
Email: info@tsuntec.com
Telephone:+86 150 6396 2790
whatsapp: 8615063962790
Address:No 2 South Hei Long Jiang Road, Shibei District, Qingdao, China