News and Events
•••Hot news
•••-
The key to ensure the long-term stable operation of the standard inverter DC arc welding machine
-
Welding Parameters Optimization and quality Control of Stainless Steel MIG Welding Wire
-
Advancements in Welding Electrode Technology and Their Impact on the Industry
-
Troubleshooting Common Issues with Welding Electrodes and Their Solutions
-
An In-depth Look into the Raw Materials and Manufacturing Processes of Carbon Steel MIG Welding Wires
Welding Parameters Optimization and quality Control of Stainless Steel MIG Welding Wire
Nov 29,2024
In the realm of stainless steel welding, MIG (Metal Inert Gas) welding is a widely adopted technique due to its versatility, speed, and ability to produce high-quality welds. The success of a MIG welding operation, especially when using stainless steel welding wire, largely depends on the careful selection and optimization of welding parameters and the implementation of stringent quality control measures.
Welding Parameters Optimization
1. Wire Diameter and Feed Rate
The diameter of the stainless steel MIG welding wire and its feed rate are crucial parameters. Thicker wires generally require higher current levels and faster feed rates, while thinner wires necessitate lower currents and slower feed rates. Proper selection ensures that the weld pool remains stable and the weld bead has a uniform appearance.
2. Welding Current and Voltage
The welding current and voltage settings must be balanced to achieve the desired penetration depth, bead width, and welding speed. Higher currents and voltages increase penetration and welding speed but may also increase the risk of burn-through or excessive heat input, which can lead to distortion or weld cracking.
3. Gas Flow Rate
The inert gas (typically argon or argon-based mixtures) used in MIG welding shields the weld pool from atmospheric contaminants. The gas flow rate should be sufficient to maintain a stable shielding environment but not excessive, as this can lead to turbulence and potential contamination.
4. Travel Speed
The speed of the welding torch along the joint line (travel speed) influences the heat input and weld quality. Too slow a speed can result in excessive heat input, weld distortion, and potential burn-through, while too fast a speed can lead to incomplete fusion and poor weld quality.
5. Contact Tip to Work Distance
The distance between the contact tip of the welding gun and the work surface (contact tip to work distance) affects the arc stability and welding current. Maintaining an optimal distance ensures stable arc performance and consistent weld quality.
Quality Control Measures
1. Pre-Weld Preparation
Proper cleaning and preparation of the welding surfaces are essential to prevent contamination and ensure good weld quality. This includes removing grease, oil, rust, and other contaminants from the surfaces to be welded.
2. Weld Inspection
Regular inspections of welds should be conducted to check for defects such as cracks, porosity, undercut, and excessive spatter. Visual inspection, magnetic particle inspection, and ultrasonic testing are common methods used for this purpose.
3. Weld Testing
Mechanical testing, such as tensile testing, bend testing, and impact testing, can provide valuable information about the strength, ductility, and toughness of the welded joints. These tests help ensure that the welds meet the specified requirements for the application.
4. Documentation and Traceability
Maintaining accurate records of welding parameters, welding consumables used, and weld test results is crucial for traceability and quality assurance. This information can be used to troubleshoot issues and improve welding processes.
5. Welder Training and Qualification
Ensuring that welders are properly trained and qualified to perform stainless steel MIG welding is essential for consistent weld quality. Regular training and qualification testing help maintain welder proficiency and improve welding outcomes.
In conclusion, optimizing welding parameters and implementing rigorous quality control measures are critical for achieving high-quality stainless steel MIG welds. By carefully selecting and adjusting welding parameters and adhering to best practices for pre-weld preparation, weld inspection, and documentation, welders can produce strong, reliable, and visually appealing welds that meet or exceed the specified requirements for their applications.
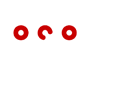
And what can we do for you?
Do you have questions about the cetecom advanced services, are you interested in a consultation or would you like to get a concrete offer? Just contact us directly. Our team of experts is looking forward to your message.

We offer a variety of top-quality welding consumables, welding accessories, welding machine for shipbuilding, aviation, nuclear power, pipeline, pressure vessel, steel structure, container, engineering machinery etc.
- Products Welding Consumables Welding Machine
- Solutions Welding Consumables Welding Machine
- quick links Cases News & Events Company
-
Contact
Email: info@tsuntec.com
Telephone:+86 150 6396 2790
whatsapp: 8615063962790
Address:No 2 South Hei Long Jiang Road, Shibei District, Qingdao, China