News and Events
•••Hot news
•••-
The key to ensure the long-term stable operation of the standard inverter DC arc welding machine
-
Welding Parameters Optimization and quality Control of Stainless Steel MIG Welding Wire
-
Advancements in Welding Electrode Technology and Their Impact on the Industry
-
Troubleshooting Common Issues with Welding Electrodes and Their Solutions
-
An In-depth Look into the Raw Materials and Manufacturing Processes of Carbon Steel MIG Welding Wires
Advancements in Welding Electrode Technology and Their Impact on the Industry
Nov 29,2024
Advancements in welding electrode technology have had a significant impact on the welding industry, enhancing efficiency, quality, and versatility in welding processes. Here are some key advancements and their implications:
1. Improved Material Composition
High-Strength Alloys: The development of new electrode materials with higher tensile strengths and improved corrosion resistance has allowed for stronger and more durable welds. These electrodes are particularly useful in applications requiring high structural integrity, such as aerospace and automotive manufacturing.
Composite Materials: Composite electrodes, such as those incorporating ceramic or metal matrix composites, offer enhanced wear resistance and better arc stability. This results in longer electrode life and reduced downtime for electrode replacement.
2. Enhanced Coatings and Surface Treatments
Coatings: Coatings on welding electrodes can improve arc stability, reduce spatter, and enhance the weld bead appearance. Advances in coating technology have led to the development of coatings that are more resistant to wear and tear, extending electrode life and improving welding efficiency.
Surface Treatments: Techniques such as plasma spray coating, laser cladding, and electrospark deposition are used to apply wear-resistant and corrosion-resistant materials to electrode surfaces. These treatments improve electrode durability and performance in harsh welding environments.
3. Precision Manufacturing Techniques
Automated Manufacturing: The use of automated manufacturing processes, such as robotic welding and computer-aided design (CAD) systems, has improved the precision and consistency of electrode production. This ensures that electrodes meet stringent quality standards and perform reliably in welding applications.
Laser Cutting and Machining: Laser cutting and precision machining techniques allow for the production of electrodes with complex shapes and geometries. This enables welders to achieve more intricate and precise welds, which is particularly important in applications requiring high levels of accuracy and detail.
4. Advanced Welding Techniques
High-Frequency Induction Welding: This technique uses high-frequency electromagnetic fields to generate heat in the welding area, resulting in faster welding speeds and reduced energy consumption.
Laser Welding: Laser welding offers precise control over the welding process, allowing for narrow weld beads and reduced distortion. It is particularly useful in applications requiring high-quality welds, such as electronics and medical devices.
5. Environmental Considerations
Low-VOC Coatings: The development of low-volatile organic compound (VOC) coatings for welding electrodes reduces emissions during welding and improves workplace air quality.
Recycling and Reuse: Advances in electrode recycling technology have made it easier to recover and reuse electrode materials, reducing waste and lowering production costs.
Impact on the Industry
Increased Efficiency: Advancements in electrode technology have led to increased welding speeds and reduced downtime, resulting in higher productivity and lower costs.
Improved Quality: Enhanced electrode materials and coatings have improved weld quality, reducing the incidence of defects and increasing the reliability of welded structures.
Expanded Applications: The development of new electrode materials and welding techniques has enabled welding in a wider range of materials and applications, including those with high strength, corrosion resistance, and complex geometries.
In summary, advancements in welding electrode technology have had a profound impact on the welding industry. These advancements have led to increased efficiency, improved quality, and expanded applications, driving innovation and progress in welding technology.
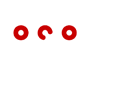
And what can we do for you?
Do you have questions about the cetecom advanced services, are you interested in a consultation or would you like to get a concrete offer? Just contact us directly. Our team of experts is looking forward to your message.

We offer a variety of top-quality welding consumables, welding accessories, welding machine for shipbuilding, aviation, nuclear power, pipeline, pressure vessel, steel structure, container, engineering machinery etc.
- Products Welding Consumables Welding Machine
- Solutions Welding Consumables Welding Machine
- quick links Cases News & Events Company
-
Contact
Email: info@tsuntec.com
Telephone:+86 150 6396 2790
whatsapp: 8615063962790
Address:No 2 South Hei Long Jiang Road, Shibei District, Qingdao, China