Welding Consumables
MIG welding wire, primarily used in Metal Inert Gas (MIG) welding, plays a crucial role in ensuring the quality and efficiency of welding processes. Below is a detailed discussion on MIG welding wire solutions.
MIG welding wires come in various types to cater to different welding needs:
Solid Wire: Typically denoted by letters such as ER (e.g., ER50-6), solid wire is suitable for welding a wide range of materials, including carbon steel and stainless steel.
Flux-Cored Wire: Flux-cored wire contains welding flux inside, which melts during welding and produces gases to protect the weld from oxidation and contamination. This type of wire is ideal for applications requiring higher welding efficiency and quality.
Selection of MIG Welding Wire
Choosing the right MIG welding wire involves considering the following factors:
Base Material Type: Select the appropriate wire based on the type of material being welded, such as carbon steel, stainless steel, aluminum alloy, etc.
Welding Requirements: Determine the welding wire based on requirements such as strength, toughness, corrosion resistance, etc.
Welding Equipment: Ensure compatibility between the selected wire and welding equipment, including welding machines and torches.
Applications of MIG Welding Wire
MIG welding wire is widely used in various welding fields, including but not limited to:
Automobile Manufacturing: For welding bodies, frames, and other components.
Machinery Manufacturing: For the manufacture and maintenance of various machinery and equipment.
Construction Engineering: For welding steel structures, bridges, and other building components.
Aerospace: For the manufacture and maintenance of aircraft, rockets, and other aerospace vehicles.
Solutions for MIG Welding Wire
To address the applications of MIG welding wire, the following solutions are provided:
Offering a Range of Wire Specifications: To meet different welding needs, a variety of wire specifications, including different diameters and materials, should be available.
Optimizing Welding Parameters: Based on the type of wire and welding requirements, optimize welding parameters such as current, voltage, and welding speed to achieve the best welding results.
Providing Technical Support and Training: Offer technical support and training to users to help them better master MIG welding techniques and wire usage.
Ensuring Wire Quality: Choose high-quality wire manufacturers to ensure that the wire quality meets relevant standards and requirements.
Precautions for Using MIG Welding Wire
When using MIG welding wire, the following precautions should be taken:
Keep the Wire Dry: Avoid exposing the wire to moisture or contamination to prevent compromising welding quality.
Proper Wire Installation: Ensure the wire is correctly installed on the welding torch to avoid knots or breaks.
Choosing the Right Welding Gas: Select the appropriate welding gas (such as argon, carbon dioxide, etc.) based on the wire type and welding requirements.
Regular Inspection of Welding Equipment: Ensure that welding equipment is in good condition to avoid equipment failures affecting welding quality.
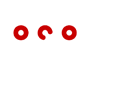
And what can we do for you?
Do you have questions about the cetecom advanced services, are you interested in a consultation or would you like to get a concrete offer? Just contact us directly. Our team of experts is looking forward to your message.

We offer a variety of top-quality welding consumables, welding accessories, welding machine for shipbuilding, aviation, nuclear power, pipeline, pressure vessel, steel structure, container, engineering machinery etc.
- Products Welding Consumables Welding Machine
- Solutions Welding Consumables Welding Machine
- quick links Cases News & Events Company
-
Contact
Email: info@tsuntec.com
Telephone:+86 150 6396 2790
whatsapp: 8615063962790
Address:No 2 South Hei Long Jiang Road, Shibei District, Qingdao, China