News and Events
•••Hot news
•••-
The key to ensure the long-term stable operation of the standard inverter DC arc welding machine
-
Welding Parameters Optimization and quality Control of Stainless Steel MIG Welding Wire
-
Advancements in Welding Electrode Technology and Their Impact on the Industry
-
Troubleshooting Common Issues with Welding Electrodes and Their Solutions
-
An In-depth Look into the Raw Materials and Manufacturing Processes of Carbon Steel MIG Welding Wires
Advantages of MIG Welding Wire
Mar 12,2025
What is MIG Welding Wire?
MIG welding wire, also known as Metal Inert Gas (MIG) welding wire, is a consumable electrode used in arc welding processes. It consists of a copper core wrapped in a protective layer of shielding flux, which is designed to protect the molten weld pool from contamination by atmospheric gases such as oxygen and nitrogen. When connected to a power source, the MIG welding wire heats up and melts, creating a molten puddle that fuses the base materials together. The inert gas (often argon or a mixture of argon and CO2) flows through the wire, providing a protective atmosphere for the weld.
MIG welding wires are available in various grades, sizes, and diameters, catering to different applications and material thicknesses. They are widely used in industries such as construction, automotive manufacturing, and pipeline engineering due to their reliability and ease of use.
Advantages of MIG Welding Wire
The MIG welding wire offers numerous advantages that make it an ideal choice for a wide range of applications, particularly in pipeline projects. Below are the key benefits:
1. High Strength and Durability
MIG welding wires are typically made from high-quality materials, such as copper and nickel alloys, which provide excellent strength and durability. The welds produced using MIG welding wires are strong and resistant to fatigue, making them ideal for applications exposed to high-stress environments, such as pipeline construction where pipes may be subject to mechanical stress due to pressure, weight, or thermal expansion.
Moreover, the shielding flux in MIG welding wires is designed to provide optimal protection against contamination, ensuring that the weld metal is clean and free from impurities. This results in strong, defect-free welds that can withstand harsh operational conditions.
2. Excellent Welding Performance
MIG welding wires are known for their excellent welding performance, thanks to their stable arc operation and consistent output. The inert gas shielding ensures a stable arc, reducing the risk of spattering or contamination during the welding process. This stability makes MIG welding wires easy to use, even for less experienced welders, and enables precise control over the welding process.
Additionally, MIG welding wires are capable of handling a wide range of material thicknesses, making them suitable for various pipeline applications, including thick-walled pipes and thin-walled pipes. The ability to handle different material gauges ensures flexibility in pipeline construction.
3. Reduced Defects
One of the most significant advantages of MIG welding wires is their ability to reduce welding defects. The inert gas shielding minimizes the likelihood of contamination, while the stable arc operation helps prevent issues such as porosity, slag inclusion, and insufficient fusion. This results in high-quality welds that are less likely to fail in service.
In pipeline projects, welding defects can lead to costly repairs and potential safety hazards. MIG welding wires help mitigate these risks by producing consistent and reliable welds, ensuring the integrity of the pipeline.
4. Ease of Use
MIG welding wires are relatively easy to use compared to other welding techniques, such as TIG (Tungsten Inert Gas) or GTAW (Gas Tungsten Arc Welding). The automated feeding mechanism eliminates the need for manual repositioning of the welding wire, reducing the risk of errors and improving efficiency. This ease of use makes MIG welding wires particularly appealing for pipeline projects where multiple welds are required in a short amount of time.
Moreover, MIG welding wires are compatible with a wide range of power sources, including constant current (CC) and pulse intelligent (PI) welders. This compatibility ensures that welders can use the same equipment for different applications, further enhancing flexibility.
5. Cost-Effective
MIG welding wires are generally more cost-effective than other welding methods, such as electron beam or laser welding, due to their lower equipment and operating costs. While MIG welding may require initial investment in specialized equipment, the long-term savings associated with high-quality welds and reduced repair costs make it a cost-efficient choice for pipeline projects.
6. Corrosion Resistance
For pipeline applications exposed to harsh environments, such as offshore drilling or chemical plants, MIG welding wires provide excellent corrosion resistance. The materials used in the welding wire are often selected based on their resistance to corrosive substances, ensuring that the welds remain intact over time. This is critical for pipelines that may be subject to environmental degradation, as well as those handling hazardous or corrosive fluids.
7. Good Assemblies and Less Spatter
MIG welding wires are known for producing good assemblies with minimal spatter. The controlled arc operation ensures that the molten weld pool is contained within the puddle, reducing the risk of scattered particles. This not only improves the quality of the weld but also reduces the amount of cleanup required post-welding.
8. Widely Applicable
MIG welding wires are widely applicable to a variety of materials, including steel, stainless steel, aluminum, and nickel alloys. Their versatility makes them suitable for different pipeline construction projects, whether the material is carbon steel or a more advanced alloy.
9. Reduced Welding Time
The automated feeding mechanism of MIG welding wires reduces the amount of time required to complete a weld, especially when compared to manual welding techniques. This increased efficiency allows welders to complete multiple tasks in a shorter amount of time, which is particularly beneficial for large pipeline projects with tight deadlines.
10. Environmental and Safety Benefits
MIG welding wires contribute to environmental safety by reducing the risk of weld-related incidents. The stable arc operation and minimal spatter make MIG welding a safer option for pipeline construction, especially in environments where worker safety is a priority. Additionally, the reduced use of consumables and waste materials can minimize the environmental impact associated with welding operations.
Applications of MIG Welding Wires in Pipeline Construction
MIG welding wires are extensively used in pipeline construction due to their versatility and reliability. They are commonly employed in:
Onshore Pipelines: For assembling pipe sections in onshore terminals or storage facilities.
Offshore Pipelines: For underwater welding, where MIG welding wires can be used with specialized equipment to ensure high-quality welds in challenging environments.
Oil and Gas pipelines: For welding pipes that may be exposed to extreme temperatures, pressure, or corrosive fluids.
Conclusion
The advantages of MIG welding wires, such as their high strength, ease of use, and reliability, make them an excellent choice for pipeline construction projects. Their ability to handle a wide range of materials, their cost-effectiveness, and their reduced risk of welding defects ensure that MIG welding wires remain a popular option for welders and engineering companies alike.
By selecting the right grade of MIG welding wire for the specific material and application, engineers and welders can ensure that pipeline projects are completed efficiently and to the highest standards of quality and safety.
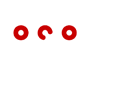
And what can we do for you?
Do you have questions about the cetecom advanced services, are you interested in a consultation or would you like to get a concrete offer? Just contact us directly. Our team of experts is looking forward to your message.

We offer a variety of top-quality welding consumables, welding accessories, welding machine for shipbuilding, aviation, nuclear power, pipeline, pressure vessel, steel structure, container, engineering machinery etc.
- Products Welding Consumables Welding Machine
- Solutions Welding Consumables Welding Machine
- quick links Cases News & Events Company
-
Contact
Email: info@tsuntec.com
Telephone:+86 150 6396 2790
whatsapp: 8615063962790
Address:No 2 South Hei Long Jiang Road, Shibei District, Qingdao, China