News and Events
•••Hot news
•••-
The key to ensure the long-term stable operation of the standard inverter DC arc welding machine
-
Welding Parameters Optimization and quality Control of Stainless Steel MIG Welding Wire
-
Advancements in Welding Electrode Technology and Their Impact on the Industry
-
Troubleshooting Common Issues with Welding Electrodes and Their Solutions
-
An In-depth Look into the Raw Materials and Manufacturing Processes of Carbon Steel MIG Welding Wires
The key to ensure the long-term stable operation of the standard inverter DC arc welding machine
Nov 29,2024
Ensuring the long-term stable operation of a standard inverter DC arc welding machine involves several critical factors that, when properly managed and maintained, can significantly extend the lifespan and reliability of the equipment. Here are the key elements to consider:
1. Proper Ventilation and Cooling
Inverter welding machines, particularly those operating at high power levels, generate significant heat. Proper ventilation and cooling systems are essential to dissipate this heat and prevent overheating, which can damage internal components. Regularly clean the cooling fans and vents to ensure they are not obstructed by dust or debris.
2. Regular Maintenance and Inspections
A preventive maintenance schedule that includes regular inspections and cleaning of the welding machine is crucial. Check for signs of wear and tear on cables, connectors, and internal components. Replace worn-out parts promptly to avoid potential failures.
3. Use of Quality Consumables
The quality of welding consumables, such as electrodes and welding wire, directly affects the performance and lifespan of the welding machine. Using high-quality consumables reduces the risk of arc instability, electrode sticking, and other issues that can stress the machine.
4. Optimal Welding Parameters
Setting the correct welding parameters (such as welding current, voltage, and welding speed) is essential for achieving good weld quality and minimizing stress on the welding machine. Incorrect parameters can lead to overheating, arc instability, and premature wear of components.
5. Consistent Power Supply
A stable and consistent power supply is critical for the reliable operation of any welding machine. Voltage fluctuations or power outages can damage internal electronics and disrupt the welding process. Consider using a voltage stabilizer or uninterruptible power supply (UPS) to protect the welding machine from these issues.
6. Proper Storage and Handling
When not in use, store the welding machine in a dry, cool, and dust-free environment. Avoid exposing it to extreme temperatures, humidity, or corrosive environments, which can accelerate aging and corrosion of components.
7. Training and Qualification of Operators
Ensuring that operators are properly trained and qualified to use the welding machine reduces the risk of improper use or abuse, which can lead to premature wear and tear. Regular training sessions and qualification tests help maintain operator proficiency and improve welding outcomes.
8. Monitoring and Diagnostics
Modern inverter welding machines often come with built-in monitoring and diagnostic features that can alert operators to potential issues before they become critical. Regularly check these systems and respond to any alerts promptly to avoid downtime and costly repairs.
9. Compliance with Standards and Regulations
Adhering to industry standards and regulations for welding equipment ensures that the welding machine meets safety and performance requirements. Regular audits and inspections can help identify any areas that need improvement.
10. Timely Repairs and Upgrades
Despite best efforts, issues may still arise. When a problem is detected, act swiftly to repair it to prevent further damage. Consider upgrading outdated components or the entire welding machine to benefit from the latest technology and improved performance.
By addressing these key factors, you can significantly enhance the long-term stability and reliability of your standard inverter DC arc welding machine, ensuring it performs optimally and delivers consistent welding results over its entire lifespan.
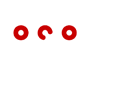
And what can we do for you?
Do you have questions about the cetecom advanced services, are you interested in a consultation or would you like to get a concrete offer? Just contact us directly. Our team of experts is looking forward to your message.

We offer a variety of top-quality welding consumables, welding accessories, welding machine for shipbuilding, aviation, nuclear power, pipeline, pressure vessel, steel structure, container, engineering machinery etc.
- Products Welding Consumables Welding Machine
- Solutions Welding Consumables Welding Machine
- quick links Cases News & Events Company
-
Contact
Email: info@tsuntec.com
Telephone:+86 150 6396 2790
whatsapp: 8615063962790
Address:No 2 South Hei Long Jiang Road, Shibei District, Qingdao, China