News and Events
•••Hot news
•••-
The key to ensure the long-term stable operation of the standard inverter DC arc welding machine
-
Welding Parameters Optimization and quality Control of Stainless Steel MIG Welding Wire
-
Advancements in Welding Electrode Technology and Their Impact on the Industry
-
Troubleshooting Common Issues with Welding Electrodes and Their Solutions
-
An In-depth Look into the Raw Materials and Manufacturing Processes of Carbon Steel MIG Welding Wires
ER70S-6 Welding Wire: A Comprehensive Guide
Feb 20,2025
Introduction
In the ever-evolving world of manufacturing and electronics, the choice of materials plays a pivotal role in determining the quality, reliability, and performance of a product. Among these materials, ER70S-6 stands out as a premium option for welding applications, particularly in the fields of electrical appliances, automotive industries, and medical devices. This article delves into the intricate details of ER70S-6 welding wire, exploring its unique characteristics, versatile applications, and essential usage guidelines.
Understanding ER70S-6 Welding Wire
ER70S-6 is a type of coated steel welding wire that has gained significant popularity in industries demanding high-quality welds. The name "ER70S-6" signifies the wire's composition and classification:
ER (Electrodeposit): Indicates that the welding wire is produced using an electrode process, ensuring consistent quality.
70S: Refers to the base metal's strength properties, with "70" representing tensile strength in pounds per square inch.
6: Denotes theclassification of the wire's coating, which is typically a basic flux-coated material.
Chemical Composition:
ER70S-6 is primarily composed of carbon steel, with additional elements such as manganese and silicon to enhance its mechanical properties. The exact composition may vary slightly depending on the manufacturer, but it generally meets industry standards for welding applications.
Key Characteristics:
High Tensile Strength: ER70S-6 exhibits exceptional strength, making it ideal for high-stress environments.
Good Weldability: The wire is easily welded using both manual and automatic welding processes, ensuring consistent and strong welds.
Durability and Corrosion Resistance: Its resistance to wear and corrosion makes it suitable for outdoor and demanding industrial settings.
Cost-Effectiveness: Despite its premium quality, ER70S-6 often offers a competitive cost compared to other high-performance materials.
2. Applications of ER70S-6 Welding Wire
ER70S-6 welding wire has a wide range of applications due to its versatility and strength. Below are some key sectors where it is widely used:
2.1 Electrical Appliances
In the production of electrical appliances, ER70S-6 is frequently employed in assembling components such as switches, sockets, and circuit breakers. Its high tensile strength ensures that the welds remain intact even under repeated stress.
2.2 Automotive Industry
The automotive sector benefits from ER70S-6's excellent mechanical properties. It is commonly used for welding frames, chassis components, and other structural parts where high strength is critical.
2.3 Medical Devices
Due to its high standards of purity and durability, ER70S-6 is a preferred material in the manufacturing of medical devices such as surgical instruments, prosthetics, and implants. Its resistance to corrosion ensures longevity and reliability in these critical applications.
2.4 Energy Storage and Infrastructure
ER70S-6 finds application in the production of batteries and energy storage systems. Its strong bonds and resistance to fatigue make it a reliable choice for high-stress environments.
3. Usage Guidelines for ER70S-6 Welding Wire
While ER70S-6 is renowned for its quality, proper usage is essential to maximize performance and minimize operational risks. Below are key guidelines for handling and welding this wire:
3.1 Pre-Welding Preparation
Cleaning: Ensure the base metal is free from oil, grease, and contamination that may affect weld quality.
Surface Preparation: Degrease or blast clean the surface to remove any irregularities.
3.2 Welding Parameters
Wire Feed Speed: Adjust according to the specific welding process (e.g., MIG, TIG) and base metal thickness.
Current Setting: Optimize based on the wire's amperage rating to achieve desired arc characteristics.
3.3 Post-Welding Treatments
Cooling: Allow the welded structure to cool naturally before performing any post-weld inspections or treatments.
Inspection: Conduct thorough visual and radiographic checks to ensure weld integrity.
3.4 Storage and Handling
Drying: Store the ER70S-6 welding wire in a dry, shaded area to prevent oxidation and contamination.
Handling: Use appropriate PPE to avoid skin contact and ensure safe handling practices.
4. Safety and Environmental Considerations
When working with ER70S-6 welding wire, it is crucial to prioritize safety and environmental sustainability:
4.1 Health and Safety
Ventilation: Ensure adequate ventilation in enclosed spaces to prevent inhalation of fumes or gases.
Electrical Safety: Use approved equipment and follow safety protocols to minimize the risk of electric shock.
4.2 Environmental Impact
Waste Management: Proper disposal of welding wire and slag according to local regulations and environmental standards.
Energy Efficiency: Optimize welding processes to reduce energy consumption and minimize environmental impact.
5. Conclusion
ER70S-6 welding wire is a top-tier choice for manufacturers seeking high-performance solutions in a variety of industries. Its exceptional strength, weldability, and durability make it an invaluable material for both industrial and specialized applications. By adhering to proper usage guidelines and prioritizing safety and environmental considerations, professionals can maximize the benefits of ER70S-6 while contributing to sustainable practices.
6. Final Thoughts
The adoption of ER70S-6 welding wire represents a commitment to quality and efficiency in manufacturing processes. Its versatility across industries underscores its importance as a reliable material for today's demanding markets. As technology continues to advance, the demand for high-performance materials like ER70S-6 is expected to grow, driving innovation and productivity in manufacturing sectors worldwide.
If you have any further questions or need detailed technical specifications, please consult with welding experts or refer to manufacturer guidelines.
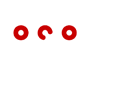
And what can we do for you?
Do you have questions about the cetecom advanced services, are you interested in a consultation or would you like to get a concrete offer? Just contact us directly. Our team of experts is looking forward to your message.

We offer a variety of top-quality welding consumables, welding accessories, welding machine for shipbuilding, aviation, nuclear power, pipeline, pressure vessel, steel structure, container, engineering machinery etc.
- Products Welding Consumables Welding Machine
- Solutions Welding Consumables Welding Machine
- quick links Cases News & Events Company
-
Contact
Email: info@tsuntec.com
Telephone:+86 150 6396 2790
whatsapp: 8615063962790
Address:No 2 South Hei Long Jiang Road, Shibei District, Qingdao, China