Aluminium Alloy Industrial Application
Dec 02,2024
Aluminum alloy properties
Aluminium is a very light metal with a density of only 2.7g/cm3, which is about 36% of the density of steel. The use of aluminum alloy to manufacture mechanical parts can significantly reduce weight and achieve the effect of light weight, energy saving and emission reduction.
The specific strength and specific stiffness of aluminum alloy are higher than 45 steel and ABS plastic. The use of aluminum alloy materials is conducive to the manufacture of monolithic components with high rigidity requirements.
Aluminum alloys have excellent thermal conductivity, electrical conductivity and corrosion resistance. Aluminum alloy has good machinability and recyclability.
Is aluminum welding difficult?
Aluminum is a soft and malleable metal. It has a lower strength for most structures. To improve the strength of aluminum, alloying elements must be added, with copper, silicon, manganese, magnesium and zinc as the main additives to play a role in solution strengthening. Aluminum and its alloys are widely used in many industries.
Aluminum and aluminum alloys are more difficult to weld than mild steel, and their welding characteristics are also different from those of mild steel. The specific performance is as follows:
1. The mechanical properties of welded joints are softened and the corrosion resistance is reduced.
2. The chemical activity is very strong, and the surface is easy to form a refractory oxide film.
3. Strong thermal conductivity, easy to cause insoluble during welding.
4. It is prone to defects such as porosity, cracks, undercuts, slag inclusions, and poor weld forming.
5. The linear expansion coefficient is large (about 2 times that of low carbon steel), and it is easy to warp and deform during welding.
6. The thermal conductivity is large (about 5 times that of mild steel), and the heat input is 2~4 times larger than that of welded steel at the same welding speed.
Classification of aluminum alloy welding technology
With the expansion of the application range of aluminum alloy, more and more problems have come to the fore. With the progress of research, the welding technology of aluminum alloy has been greatly developed. At present, there are mainly tungsten argon arc welding (TIG), melting electrode inert gas shielded welding (MIG), laser welding (LBW), friction stir welding (FSW) and so on.
Tungsten Inert Gas Welding (TIG) is a typical inert gas welding and is the most commonly used welding method. During welding, the tungsten electrode and the welding surface are used as the electrodes, and helium or argon is passed between the two electrodes as a shielding gas to protect the arc, and the welding wire and base metal are melted through instantaneous high-voltage discharge, and the welding and forming of aluminum alloy parts, and the welding and repair of casting defects.
It mainly has the following technical characteristics:
1. Easy to operate, flexible and controllable, adapt to various working conditions and environments, and low cost;
2. The heat affected zone is narrow, the deformation of the welded joint is small under the condition of sufficient wire feeding, and the comprehensive performance of the joint is high;
3. The welding process performance is good and stable, and the weld is dense and beautiful.
MIG (GMA - Gas Metal Arc Welding) and TIG are both inert gas shielded welding. The difference is that TIG welding uses a tungsten electrode as a fixed electrode, while MIG welding uses the filler wire material itself as the electrode.
In the process of aluminum alloy metal inert gas shielded welding, the voltage and current act on the electrode of the welding wire, and an instantaneous high voltage is generated between the electrode and the base metal, which melts the base metal and the base metal. The groove, the molten droplets at the end of the wire come off and transition vertically to the base metal. A weld zone is formed on the molten pool of the material.
Application process of aluminum alloy MIG welding
1. Socketing of copper and aluminum pipes in the refrigeration industry, dissimilar welding of copper and galvanized pipes, stainless steel pipes and aluminum pipes of central air conditioning.
2. Welding of copper-aluminum terminals, copper-aluminum leads, and copper-aluminum conductive bars in the substation industry.
3. Welding of radiator tubes, motors and bus bars in the electronic and electrical industry.
4. It is also used in the production and life of faucets, coupling connectors, matching nuts and so on.
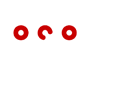
And what can we do for you?
Do you have questions about the cetecom advanced services, are you interested in a consultation or would you like to get a concrete offer? Just contact us directly. Our team of experts is looking forward to your message.

We offer a variety of top-quality welding consumables, welding accessories, welding machine for shipbuilding, aviation, nuclear power, pipeline, pressure vessel, steel structure, container, engineering machinery etc.
- Products Welding Consumables Welding Machine
- Solutions Welding Consumables Welding Machine
- quick links Cases News & Events Company
-
Contact
Email: info@tsuntec.com
Telephone:+86 150 6396 2790
whatsapp: 8615063962790
Address:No 2 South Hei Long Jiang Road, Shibei District, Qingdao, China